THE KAVON RESOURCE CENTER
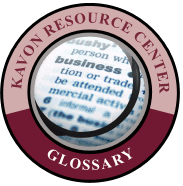 |
Glossary of Terms
The Glossary Of Terms provide definitions to commonly used words in various business environments.
You can view glossary terms by Term, Acronym, Category, or as a Complete List of Terms or a Complete List of Aconyms.
If you have any other terms that you would like us to include, contact us and we will consider adding it to our glossary. |
5S |
|
5S |
|
One of the lean tool sets for creating work place organization (Sort, Straighten, Shine, Standardize, and Sustain). |
|
|
|
|
|
|
5S+1 |
|
5S+1 |
|
One of the lean tool sets for creating work place organization including safety (Sort, Straighten, Shine, Standardize, and Sustain + Safety). |
|
|
|
|
|
|
ANOVA |
|
Analysis Of Variance |
|
A statistical method to determine if a statistical difference is detectable between the averages of multiple samples. |
|
|
|
|
|
|
AIAG |
|
Automotive Industry Action Group |
|
The AIAG (Automotive Industry Action Group) is a non-profit association of automotive companies founded in 1982. |
|
|
|
|
|
|
DTD |
|
Dock To Dock |
|
A lean performance measurement counting amounts of in-process inventory (WIP) and converting it to days of inventory between receiving raw material and shipping the finished product (a measurement of product velocity). |
|
|
|
|
|
|
DBR |
|
Drum-Buffer-Rope |
|
Drum-Buffer-Rope is a manufacturing execution methodology, named for its three components.
- Drum: The physical constraint of the plant: the work center or machine or operation that limits the ability of the entire system to produce more. The rest of the plant follows the beat of the drum. They make sure the drum has work and that anything the drum has processed does not get wasted.
- Buffer: Protects the drum, so that it always has work flowing to it. Buffers in DBR have time as their unit of measure, rather than quantity of material. This makes the priority system operate strictly based on the time an order is expected to be at the drum. Traditional DBR usually calls for buffers at several points in the system: the constraint, synchronization points and at shipping.
- Rope: The work release mechanism for the plant. Orders are released to the shop floor at one "buffer time" before they are due. In other words, if the buffer is 5 days, the order is released 5 days before it is due at the constraint. Putting work into the system earlier than this buffer time is likely to generate too-high work-in-process and slow down the entire system.
|
Source: "Theory of Constraints" Wikipedia http://en.wikipedia.org. Web. 04 October 2011.
http://en.wikipedia.org/wiki/Theory_of_Constraints
|
|
|
|
|
|
EMS |
|
Environmental Management System |
|
Part of an organization's management system used to develop and implement its environmental policy and manage its environmental aspects.
NOTE 1: A managment system is a set of interrelated elements used to establish policy and objectives and to acheive those objectives.
NOTE 2: A managment system includes organizational structure, planning activities, responsibilities, practices, procedures, processes and resources. |
Source: ASQ. ISO 14001:2000 - Environmental Management Systems - Requirements With Guidance For Use. Milwaukee, WI: Quality Press, 15 Nov. 2004. PDF.
|
|
|
|
|
|
FIFO |
|
First In First Out |
|
First In First Out, FIFO lanes can be used between two (2) decoupled processes to substitute for a super market, and maintained by flow between them. |
|
|
|
|
|
|
FTT |
|
First Time Through |
|
First Time Through. A lean performance measurement, the actual percentage (%) loss of raw material as it proceeds through the manufacturing process. This includes all loss, such as nonconforming product, scrap, setup pieces, lab tests, etc. |
|
|
|
|
|
|
GRR
GR&R |
|
Gage Repeatability and Reproducibility |
|
An estimate of the combined variation of repeatability and reproducibility for a measurement system. The GRR variance is equal to the sum of within-system and between-system variances. |
Source: DaimlerChrysler Corporation/Ford Motor Company/General Motors Corporation Supplier Quality Requirements Task Force. Measurement Systems Analysis - Reference Manual (Third Edition). Southfield, MI: AIAG, March 2002, p. 206.
|
|
|
|
|
|
ISO |
|
International Organization for Standardization |
|
ISO (International Organization for Standardization) is the world's largest developer and publisher of International Standards.
ISO is a network of the national standards institutes of 162 countries, one member per country, with a Central Secretariat in Geneva, Switzerland, that coordinates the system.
ISO is a non-governmental organization that forms a bridge between the public and private sectors. On the one hand, many of its member institutes are part of the governmental structure of their countries, or are mandated by their government. On the other hand, other members have their roots uniquely in the private sector, having been set up by national partnerships of industry associations.
Therefore, ISO enables a consensus to be reached on solutions that meet both the requirements of business and the broader needs of society.
ISO's Name
Because "International Organization for Standardization" would have different acronyms in different languages ("IOS" in English, "OIN" in French for Organisation internationale de normalisation), its founders decided to give it also a short, all-purpose name. They chose "ISO", derived from the Greek isos, meaning "equal". Whatever the country, whatever the language, the short form of the organization's name is always ISO. |
Source: http://www.iso.org/iso/about.htm
http://www.iso.org/iso/about/discover-iso_isos-name.htm
|
|
|
|
|
|
JI |
|
Job Instruction Training |
|
One of the four programs that make up Training Within Industry. Trains workers in how to instruct a person to perform a job correctly and safely; and to be productive as quickly as possible, while creating less scrap, rework, and damage to tools and equipment. |
Source: Donald A. Dinero, Training Within Industry, The foundation of Lean, Productivity Press 2005, p. 3.
|
|
|
|
|
|
JM |
|
Job Methods Training |
|
One of the four programs that make up Training Within Industry. Trains employees in how to improve the way jobs are performed in order to consistently produce greater quantities of quality products in less time using the available manpower, machines, and materials. |
Source: Donald A. Dinero, Training Within Industry, The foundation of Lean, Productivity Press 2005, p. 4.
|
|
|
|
|
|
JR |
|
Job Relations Trainng |
|
One of the four programs that make up Training Within Industry. Trains employees in how to solve personal problems using an analytical, nonemotional method combined with some basic foundations of human relations. JR emphasizes that you must treat all people as individuals and be understanding people on all levels, supervisors can achieve results working through people. |
Source: Donald A. Dinero, Training Within Industry, The foundation of Lean, Productivity Press 2005, p. 3.
|
|
|
|
|
|
JIT |
|
Just-In-Time |
|
Just-In-Time manufacturing is a philosophy that says we use inventory and manufacture items as they are needed or just-in-time. Holding inventories is wrong and producing long manufacturing runs and storing items in finished goods inventory is wasteful, and prevents firms from adopting to changing customer needs. |
Source: Peter Mears, Quality Improvement - Tools & Techniques, McGraw-Hill, Inc. 1995, p. 210.
|
|
|
|
|
|
MBNQA |
|
Malcolm Baldrige National Quality Award |
|
A U.S. national quality award sponsored by the U.S. Department of Commerce and private industry. The award is named after former Secretary of Commerce Malcolm Baldrige. |
|
|
|
|
|
|
MAIC |
|
Measure, Analyze, Improve, Control |
|
Measure, Analyze, Improve, Control. This is the steps of Six Sigma. |
|
|
|
|
|
|
MSA |
|
Measurement System Analysis |
|
Measurement System Analysis (MSA) is a specially designed experiment that seeks to identify the components of variation in the measurement.
A Measurement Systems Analysis evaluates the test method, measuring instruments, and the entire process of obtaining measurements to ensure the integrity of data used for analysis (usually quality analysis) and to understand the implications of measurement error for decisions made about a product or process.
A Measurement Systems Analysis considers the following:
- Selecting the correct measurement and approach
- Assessing the measuring device
- Assessing procedures & operators
- Assessing any measurement interactions
- Calculating the measurement uncertainty of individual measurement devices and/or measurement systems
|
Source: "Measurement system analysis" Wikipedia http://en.wikipedia.org. Web. 04 October 2011.
http://en.wikipedia.org/wiki/Measurement_systems_analysis
|
|
|
|
|
|
OEE |
|
Overall Equipment Effectiveness |
|
Overall Equipment Effectiveness. A lean performance metric organized to measure machine up time and decompose reasons for down time. Measured in percentage (%), with 85% being considered "World Class Performance". |
|
|
|
|
|
|
PDCA |
|
Plan Do Check Act |
|
The Plan-Do-Check-Act (PDCA) is a well-known model for continual process improvement. It teaches organizations to Plan an action, Do it, Check to see how it conforms to the plan and Act on what has been learned.
The PDCA Cycle consists of the following four steps:
- Plan: Recognize an opportunity and plan the change.
- Do: Test the change.
- Check: Review the test, analyze the results and identify what was learned.
- Act: Take action based on what was learned in the check step. If the change was successful, incorporate what was learned from the test into wider changes. If not, go through the cycle again with a different plan.
The PDCA Cycle is also know as the Shewhart Cycle and Deming Cycle. Walter A. Shewhart first discussed the concept of PDCA in his 1939 book, Statistical Method From the Viewpoint of Quality Control.
W. Edwards Deming is credited with encouraging the Japanese in the 1950s to adopt PDCA. The Japanese eagerly embraced PDCA and to honor Deming for his instruction, they refer to the PDCA Cycle as the Deming Cycle. |
|
|
|
|
|
|
PIE |
|
Process Improvement Event |
|
In healthcare, another name for a Kaizen Event. |
Source: Mark Graban, Lean Hospitals, Improving Quality, Patient Safety, Employee Satisfaction, Ortho-Clinical Diagnostics, Inc. 2009, p. 207.
|
|
|
|
|
|
PD |
|
Program Development |
|
One of the four programs that make up Training Within Industry. Trains employees to solve production problems that were unique to their organization. PD solves problems related to personnel through training while problems related to other resources are solved through technical means. |
Source: Donald A. Dinero, Training Within Industry, The foundation of Lean, Productivity Press 2005, p. 4.
|
|
|
|
|
|
QFD |
|
Quality Function Deployment |
|
Quality Function Deployment (QFD) is an advanced form of customer needs mapping which encourages users to focus on the broader process of how results are obtained. QFD was developed by the Japanese in 1972. It is a formal process for translating customer requirements into appropriate technical requirements. QFD is used to assure that all of a company's operations are driven by the customer's needs, rather than by top management (or by design engineers).
The attached image represents an example of a QFD House of Quality matrix. |
Source: Peter Mears, Quality Improvement - Tools & Techniques, McGraw-Hill, Inc. 1995, p. 165.
|
|
|
|
|
|
RPIW |
|
Rapid Process Improvement Workshop |
|
In healthcare, another name for a Kaizen Event. |
Source: Mark Graban, Lean Hospitals, Improving Quality, Patient Safety, Employee Satisfaction, Ortho-Clinical Diagnostics, Inc. 2009, p. 207.
|
|
|
|
|
|
RCDQ |
|
Reactive Customer-Driven Quality |
|
A state that is characterized by a supplier "reacting" to the quality expectations of a customer rather than proactively anticipating customer needs and expectations. |
|
|
|
|
|
|
SME |
|
Subject Matter Expert |
|
A person who has intimate knowledge or expertise of a particular area, topic or process. Individuals who are involved in the day to day activities of a process is sometimes referred to as a subject matter expert and a such is asked to participate as part of team charged with improving the process. |
|
|
|
|
|
|
TOC |
|
Theory Of Constraints |
|
Theory of Constraints (TOC) is an overall management philosophy introduced by Dr. Eliyahu M. Goldratt in his 1984 book titled The Goal, that is geared to help organizations continually achieve their goals.[1] Dr. Eliyahu M. Goldratt adopted the concept with his book Critical Chain, published 1997. The concept was extended to TOC with respectively titled publication in 1999.
The title Theory of Constraints (TOC) adopts the common idiom "A chain is no stronger than its weakest link" as a new management paradigm. This means that processes, organisations, etc., are vulnerable because the weakest person or part can always damage or break them or at least adversely affect the outcome.
The analytic approach with TOC comes from the contention that any manageable system is limited in achieving more of its goals by a very small number of constraints, and that there is always at least one constraint. Hence the TOC process seeks to identify the constraint and restructure the rest of the organization around it, through the use of Five Focusing Steps.
|
Source: "Theory of Constraints" Wikipedia http://en.wikipedia.org. Web. 04 October 2011.
http://en.wikipedia.org/wiki/Theory_of_Constraints
|
|
|
|
|
|
TWI |
|
Training Within Industry |
|
Also referred to as TWI, it is a program which uses a learn-by-doing approach, teaching essential skills for supervisors and team leaders. Its four core elements are:
- Job Relations
- Job Instruction
- Job Methods
- Program Development
Its roots go back to the Training Within Industry service created by the U.S. Department of War in 1940. |
|
|
|
|
|
|
VOB |
|
Voice Of The Business |
|
The Voice Of The Business represents the needs of the business and its key stakeholders. These needs include items like; profitability, revenue, growth, market share, etc. |
|
|
|
|
|
|
VOC |
|
Voice Of The Customer |
|
A phrase that refers to the range of results that are acceptable to a customer, whether in the form of a numeric specification or verbal feedback. |
|
|
|
|
|
|
VOP |
|
Voice Of The Process |
|
A phrase that refers to the range of results that are produced by a process. |
|
|
|
|
|
|
|

|
|