The Youngstown-Warren Section (#805) of the American Society For Quality held their monthly meeting on March 14, 2011 at the Kent State University Stark campus in Trumbull, Ohio. The featured speaker was John Novak, president of KAVON International, Inc. and a Certified Lean Six Sigma Master Black Belt. John facilitated both the Technical Clinic and the dinner meeting.
Technical Clinic
During the Technical Clinic, John demonstrated the use of Quality Companion (from Minitab) as a tool to manage, track and document continual improvement projects using the DMAIC methodology. He covered the following features:
- Setting up a DMAIC project roadmap
- Creating a custom project roadmap
- Establishing a project charter
- Creating Process Maps
- Creating and modifying an FMEA
- Creating and loading custom templates
- Using Quality Companion coaches
- Using analysis forms to report and interpret results from a Minitab analysis
- Attaching external files to your project
- Creating a presentation
- Exporting project information to PowerPoint
- Importing Visio flowcharts
John also mentioned that a free Quality Companion Viewer can be downloaded from the Minitab website to allow anyone to view the contents of a Quality Companion project file without being able to make changes. He indicated that by placing these project files on a central network location, it would facilitate communication among all employees in an organization by allowing them to view current and completed projects and possibly contribute valuable information.
Lastly, John mentioned that a free Quality Companion Dashboard was also available as a free download from the Minitab website, which allows project managers to view the status of projects together as a group.
Dinner Meeting
During the dinner meeting, John gave a talk on,
"Exploring Audit Trails During a Process Based Internal Audit."
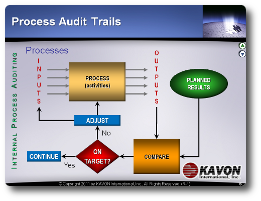
John started out by contrasting the twenty element approach of ISO 9001:1994 and the process approach of ISO 9001:2000 and ISO 9001:2008.
He talked about the process approach that was introduced in ISO 9001:2000 and gave a description of the components of a process:
- Inputs
- Activities
- Outputs
- Measures of Effectiveness
John proceeded to describe the following types of inputs he encounters when conducting an internal audit and the audit trails he follows:
Input Type |
Audit Trail |
Personnel |
Human Resources |
Documents |
Document Control Administrator |
Material |
Purchasing, Customer Specifications, or Incoming Inspection |
Equipment |
Maintenance or IT Group |
Environmental |
Production Control or Engineering |
General |
Various |
John indicated that the failure of any input can lead to the compromise of the process. In order for the process to function effectively, each of the inputs has to do its part. With that, John identified some key questions he uses to interrogate each type of input in order to determine the input’s effectiveness.
Personnel Inputs:
- What skills are required for this process?
- What skill set does the auditee possess?
- Are there any competency gaps?
- How effective has any training been?
- How could the training be improved?
Document Inputs:
- Where does the document come from?
- How does the auditee know if the document is the most current?
- Is the document the latest revision?
- Does the document clearly provide the necessary information?
- How could the document be improved?
Material Inputs:
- Where does the material come from?
- How do you know the material is correct?
- How do you know if the material composition is correct?
- Does the material documentation clearly provide the necessary information?
- How could the material be improved?
Equipment Inputs:
- Who determines the appropriate equipment to use?
- How do you know if the equipment is adequate for the job?
- Is the equipment maintained?
- What are the maintenance requirements?
- Has the maintenance been performed?
- How could the equipment be improved?
Environmental Inputs:
- Are there any environmental considerations for this process?
- How are the environmental requirements controlled & documented?
- Are the environmental requirements adequate?
- Who establishes the environmental requirements?
- How could the environmental requirements be improved?
General Inputs:
- What information do you receive in order to perform this activity?
- Where does this information come from?
- When do you get this information?
- How good is this information?
- How could this information be improved?
The final audit trails John explored were those created through the outputs. He explained how both internal and external customers had to be satisfied by the output they received. His basic questions for outputs are:
Outputs:
- What do you send on to others?
- Who are the recipients?
- How do you know if the output is complete, sufficient or correct?
- What records do you keep documenting what you did and if it was correct?
- How satisfied are the recipients of the outputs?
- How would the recipient improve what they get?
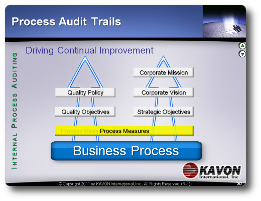
John emphasized how properly implemented process measures were critical in evaluating and monitoring processes for effectiveness. He linked good process measures directly to the attainment of the Quality Objectives and fulfillment of the Quality Policy, as well as the strategic plan. He made the case that appropriate process measures needed to be established when an internal audit found the process to be less than effective.
John then outlined some basic questions he uses when evaluating the process measures:
Measures of Effectiveness:
- What criteria do you use to determine process performance (effectiveness)?
- What is the linkage between the criteria and process performance?
- What metric(s) do you use to measure the performance based on the criteria?
- Are your measures on target?
- Is the data trending in the right direction?
- Are there ways you could better measure or improve the process?
Finally, John emphasized the importance of getting value out of the internal auditing process and supporting the continual improvement requirements of ISO 9001:2008. He left everybody with one final thought:
"A robust internal auditing program shows its presence both at the beginning and end of continual improvement projects. In the beginning, internal audits identify opportunities for improvement; at the end, internal audits provide a mechanism for monitoring the implemented improvement in order to sustain its benefits for the long term."
The session concluded with a period of questions and answers.